A brand new development in 3D printing know-how is opening doorways for numerous medical purposes, together with customized implants and coronary heart bandages. Researchers at CU Boulder, in collaboration with the College of Pennsylvania, have developed a 3D printing methodology that produces supplies which are each robust and versatile, able to adapting to the physique’s particular wants.
Progressive Materials for Medical Use
The workforce, led by Professor Jason Burdick of CU Boulder’s BioFrontiers Institute, has created a fabric that may stand up to the center’s fixed beating, endure joint stress, and conform to totally different sizes and shapes. Their findings have been revealed within the August 2 version of Science.
“Cardiac and cartilage tissues are related in that they’ve very restricted capability to restore themselves. After they’re broken, there is no such thing as a turning again,” stated Burdick. “By creating new, extra resilient supplies to boost that restore course of, we are able to have a big effect on sufferers.”
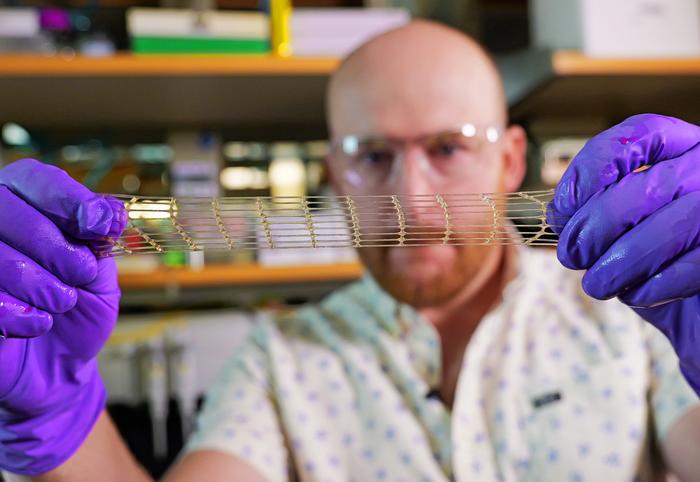
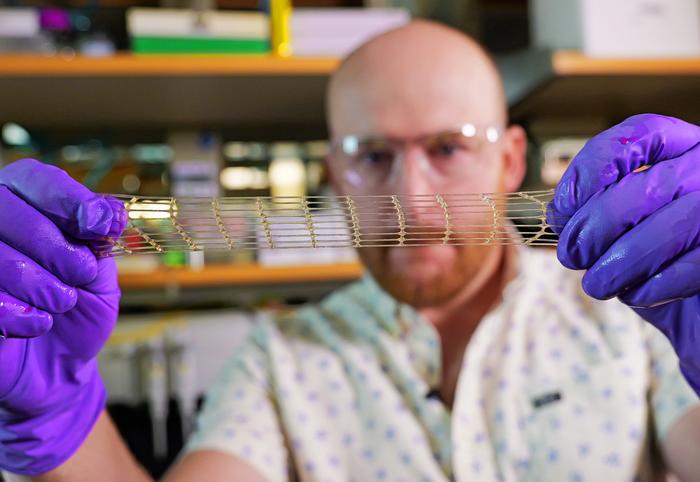
Nature-Impressed Innovation
Conventional biomedical gadgets are sometimes mass-produced, missing the pliability for customized implants. 3D printing gives an answer by enabling the creation of personalized shapes and buildings. Not like typical printers, 3D printers construct objects layer by layer utilizing supplies reminiscent of plastics, metals, and even residing cells.
Hydrogels, typically utilized in making contact lenses, have been a promising materials for synthetic tissues and implants. Nonetheless, typical 3D-printed hydrogels typically fail beneath stress, both breaking when stretched or cracking beneath stress.
Burdick’s workforce drew inspiration from worms, which type stable but versatile “blobs” by entangling themselves. By mimicking this entanglement with lengthy molecular chains, they developed a brand new printing methodology known as CLEAR (Steady-curing after Gentle Publicity Aided by Redox initiation).
Exceptional Resilience and Adhesion
Exams confirmed that supplies printed with CLEAR have been extra sturdy than these made with conventional 3D printing strategies. One researcher even ran over a pattern with a motorcycle, demonstrating its power. Moreover, these supplies adhered nicely to animal tissues and organs.
“We are able to now 3D print adhesive supplies robust sufficient to help tissue mechanically,” stated Matt Davidson, a analysis affiliate within the Burdick Lab.
Potential for Reworking Medical Care
Burdick envisions these supplies getting used to restore coronary heart defects, ship tissue-regenerating medicine on to organs, help cartilage, and even exchange conventional sutures with needle-free choices that decrease tissue harm.
The workforce has filed for a provisional patent and plans additional research to know how tissues work together with these new supplies.
Past medication, this methodology has potential purposes in analysis and manufacturing, providing a extra environmentally pleasant 3D printing course of by eliminating the necessity for added power to harden elements.
“This can be a easy 3D processing methodology that folks might in the end use in their very own educational labs in addition to in business to enhance the mechanical properties of supplies for all kinds of purposes,” stated Abhishek Dhand, a researcher within the Burdick Lab and doctoral candidate within the Division of Bioengineering on the College of Pennsylvania.
For extra detailed data, the total examine may be accessed at Science.org. The unique article is on the market at EurekAlert.