SPEE3D, a steel additive manufacturing OEM, has participated within the US Naval Sea Programs Command (NAVSEA) inaugural SALVEX train at Pearl Harbor. The operation ran in Might 2024 and sought to exhibit steel 3D printing functionality to restore injury and maintain army operations.
Primarily based in Australia, SPEE3D’s XSPEE3D and SPEE3Dcell Chilly Spray Additive Manufacturing (CSAM) have been used to 3D print crucial steel components. Navy reservists and the Naval Postgraduate College (NPS) have been tasked with utilizing on-demand steel printing in a state of affairs simulating a selected naval situation.
“SPEE3D is honored to be chosen by the US Navy as soon as once more to exhibit our proprietary cold-spray steel additive manufacturing expertise,” stated Byron Kennedy, CEO of SPEE3D “Collaborating in an train the place a ship shall be purposefully broken as a part of a naval train is novel, and we’re optimistic that XSPEE3D will be capable to print essential steel components to assist restore the vessel rapidly.
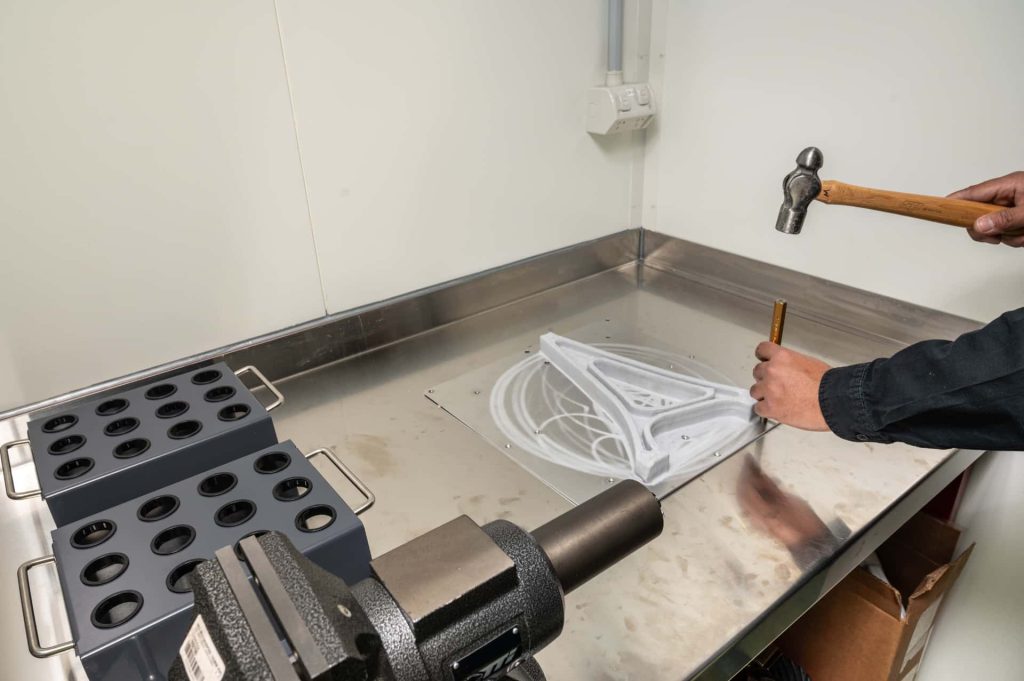
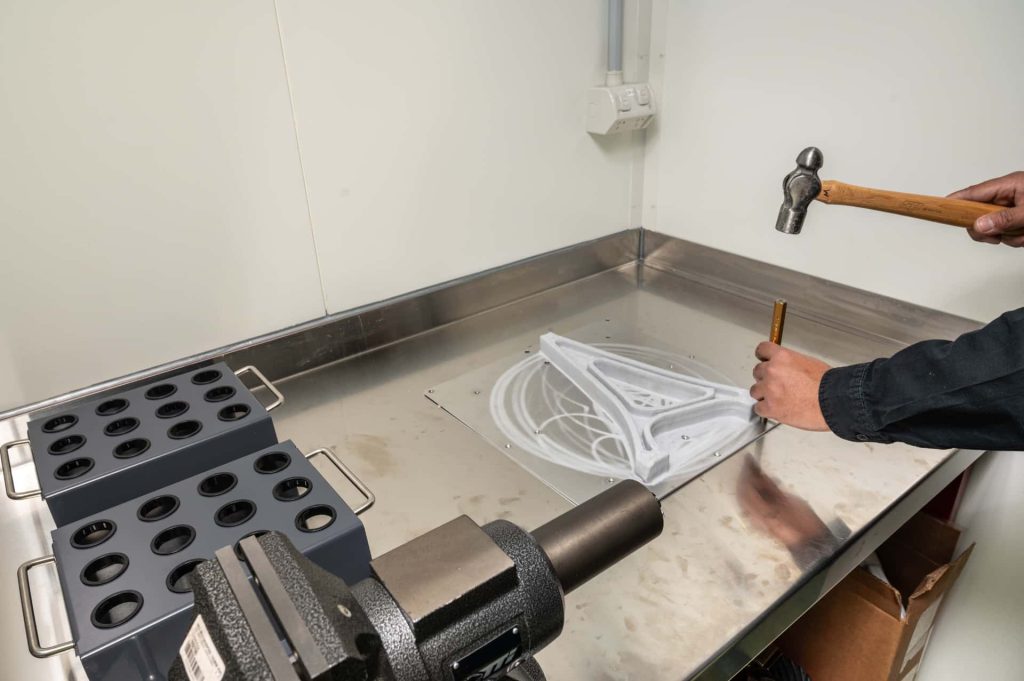
Enhancing Naval Capabilities By Additive Manufacturing
XSPEE3D is an Expeditionary Manufacturing Unit (EMU), or, in additional simple phrases – a delivery container with the gear essential to run the steel 3D printer.
This cellular additive manufacturing system is optimized for protection functions and able to printing steel components as much as 1m x 0.7m (40″ x 30″) inside hours. Materials choices embody aluminum, copper, and chrome steel. The SPEE3Dcell unit, which pairs with the XSPEE3D, features a warmth remedy furnace, CNC mill, and important tooling. CSAM, not like steel additive processes like Laser Energy Mattress Fusion or Electron Beam Melting, doesn’t require lasers or inert gases.
“Making certain the safety of our nation requires expertise that may efficiently work in all environments – together with at sea,” stated a Navy spokesperson. “Provide chain points are prevalent, so with the ability to manufacture steel components rapidly and from anyplace is a large challenge that we’re excited to check and hopefully resolve.”
“The flexibility to rapidly produce and deploy important elements is crucial for sustaining our naval forces’ operational readiness and effectiveness.” SPEED3D’s CEO famous, “Our participation within the SALVEX train demonstrates the robustness and flexibility of our additive manufacturing options, tailor-made to fulfill the rigorous calls for of naval functions.”
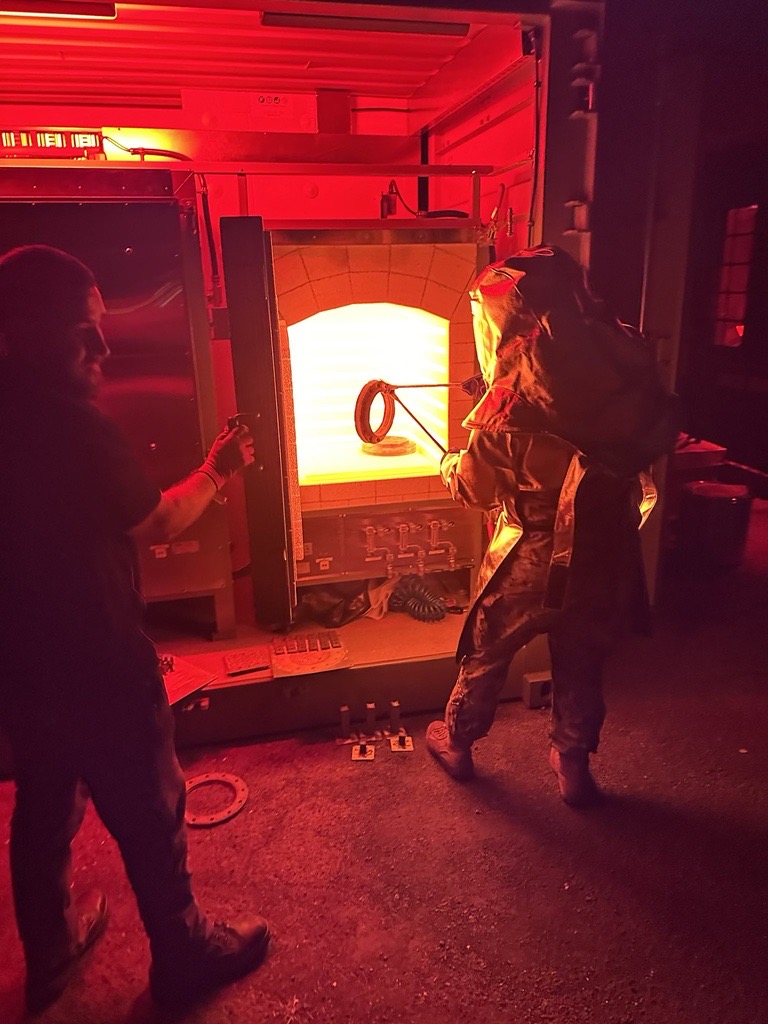
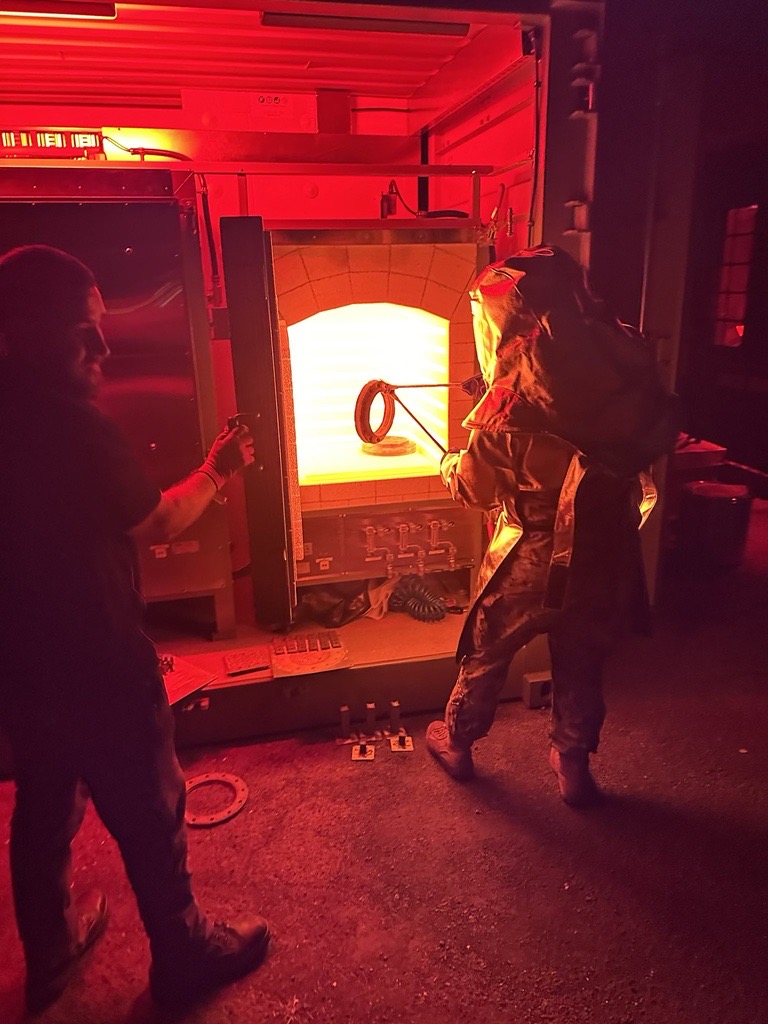
Additive Manufacturing for the Navy
More and more, steel additive manufacturing is discovering maritime functions for the U.S. Navy.
For instance, Bechtel Plant Equipment Inc. (BPMI) has chosen Velo3D’s superior steel additive manufacturing (AM) system to boost the U.S. Naval Nuclear Propulsion Program. The system, that includes the Sapphire XC giant format printer, is optimized for stainless-steel 415 and shall be operated by ATI at their new facility close to Fort Lauderdale, Florida. This integration goals to streamline the manufacturing of advanced components, beforehand made by way of casting, thus decreasing lead instances and optimizing the availability chain for crucial elements.
The collaboration between BPMI and ATI highlights the Navy’s strategic adoption of additive manufacturing to take care of its fleet, notably getting older vessels. Velo3D’s expertise, recognized for dealing with intricate geometries with minimal assist buildings, helps this initiative by enhancing manufacturing effectivity demonstrating the utility of steel 3D printing for nuclear propulsion. This growth is seen as a major step ahead in bolstering the Navy’s upkeep and operational readiness.
Elsewhere, rocket engine producer Ursa Main has secured a contract with the US Navy to design, 3D print, and hot-fire take a look at a prototype stable rocket motor (SRM) for the Commonplace Missile (SM) program. Using its additive manufacturing-powered Lynx expertise, Ursa Main goals to develop next-generation SRMs optimized for manufacturability and reliability. The 3D printed stable rocket motors venture, below the Naval Energetic Programs and Applied sciences (NEST) Program, focuses on making a 3D printable design for the Mk 104 twin rocket motor, which is integral to the SM-2, SM-3, and SM-6 missiles.
With the US going through a excessive demand for SRMs and a scarcity of home suppliers, Ursa Main’s Lynx expertise is ready to speed up and scale the manufacturing of crucial missile elements. Joe Laurienti, Founder and CEO of Ursa Main, emphasised the corporate’s functionality to quickly develop high-performance motors at scale, addressing pressing nationwide wants. The collaboration entails the US Navy’s Program Government Workplace Built-in Warfare Programs (PEO IWS) 3.0 and different naval divisions. The brand new 3D printed SRM is anticipated to enter manufacturing inside three years, considerably enhancing the Navy’s missile capabilities and industrial base.
Be a part of our on-line occasion, Additive Manufacturing Benefit: Aerospace, Area & Protection to listen to from consultants and end-users in cutting-edge verticals. Register now.
Keep updated with all the most recent information subscribe to the 3D Printing Business publication.
Comply with us on LinkedIn, Twitter and, Fb for the most recent updates. Watch previous webinars, revisit 3D printer critiques and insights from tradeshow on our YouTube channel.
Featured picture reveals A Navy Reservist working the SPEE3D Cell. Picture by way of SPEE3D.